Safety and Quality
Basic Philosophy
The KONOIKE Group corporate philosophy states that we pursue innovation at the foundations of our society that creates unique value, driven by respect for humanity and relationships of trust. Above all, we believe that safety and quality are extremely important for the bond that connects us to our customers. It is the responsibility of a company to make its earnings grow. Our growth depends on customers trusting the front lines of the KONOIKE Group. For that reason, we believe safety, quality, and business performance are three equal factors in an important trinity. We strive to create a unified awareness among all KONOIKE employees: Quality supports trust, the front lines support quality, and safety supports the front lines. In order to continue to earn the trust of our customers, we will combine quality and safety with technology, evolving these into robust strengths. In response to an environment and challenges that change moment-by-moment, we act flexibly within the scope of our annual Corporate Quality Policy, striving to ensure greater safety in operations and improved quality.
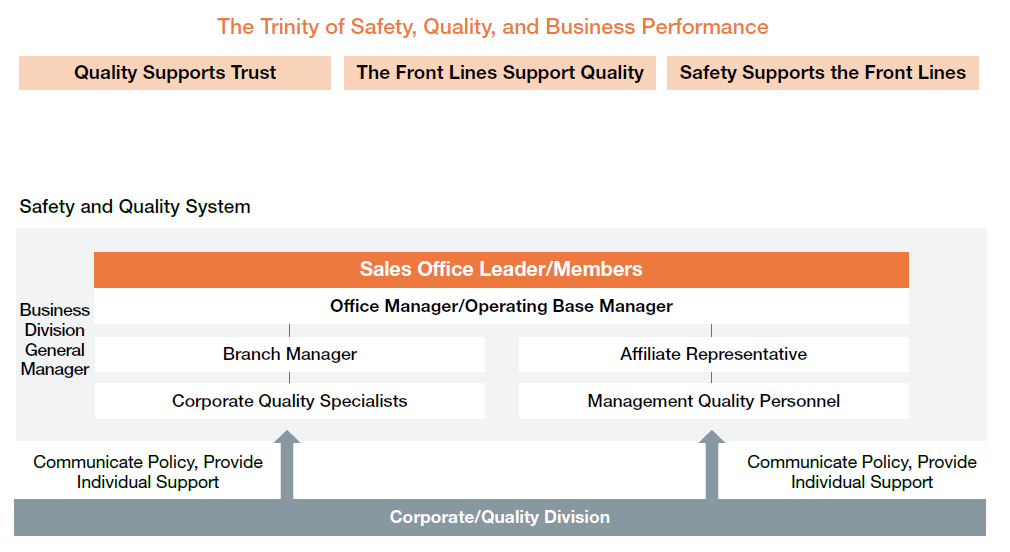
2025 Safety and Quality Policy
- Cultivate (educate) employees to anticipate hazards before acting and implement effective hazard prediction with enhanced situational awareness.
- Engage all employees in risk reduction activities (identifying near misses and other hazards→ small-group activities→ improvements).
- Share trouble case studies and implement accountability-driven recurrence prevention measures.
- Implement initiatives that support both mental and physical well-being.
- Increase front-line capabilities through self-driven safety initiatives (technological improvements).
Target | Safety | Rate of Lost Worktime Injuries (Konoike/Group Companies) | 0.23 or less |
---|---|---|---|
Rate of Incidents (Konoike/Group Companies) | 1.60 or less | ||
Partner Business Closures | 3 or less | ||
Traffic Accidents | Commercial Vehicle Accident Rate (KONOIKE/Group Company Vehicles) | 0.15 or less | |
Business-Related Vehicles/Overseas Subsidiary Accidents | 3 or less | ||
Number of Accidents at Partners | 3 or less | ||
Quality Incidents | Critical Quality Incidents (100,000 yen or more) | 22 or less |
Transportation Safety Initiatives
Safety and Quality Activity System
We conduct safety and quality activities based on the Corporate Quality Policy announced at the beginning of the year. Based on the Corporate Quality Policy of the Head Office, each sales office incorporates activities for the year into their operating plans, after which they proceed with the activities through the SDCA cycle. Once these improved methods are standardized into SDCA, the offices return to the SDCA cycle. In addition to the abovementioned daily safety activities, the Head Office Safety/ Quality Department and each corporate quality specialist and individual in charge work together to tackle individual issues each year. In FY3/2024, we continued our efforts from the previous year, working to reinvigorate initiatives concerning near-accidents. Each corporate quality specialist or individual in charge selected a location under their jurisdiction for 4M5E analysis of factors interfering with near-accident initiatives. Each specialist and individual in charge worked together with the Head Office Safety/Quality Department via web conference to check progress, including progress on items noted in the work process chart. In principle, safety and quality activities are carried out under the direction of each general manager, the branch manager and the sales office manager in order. However, each corporate quality specialist or other individual in charge assigned to a branch or affiliate receives individual support from the Corporate/Quality Division and provides support for the activities at each sales office.
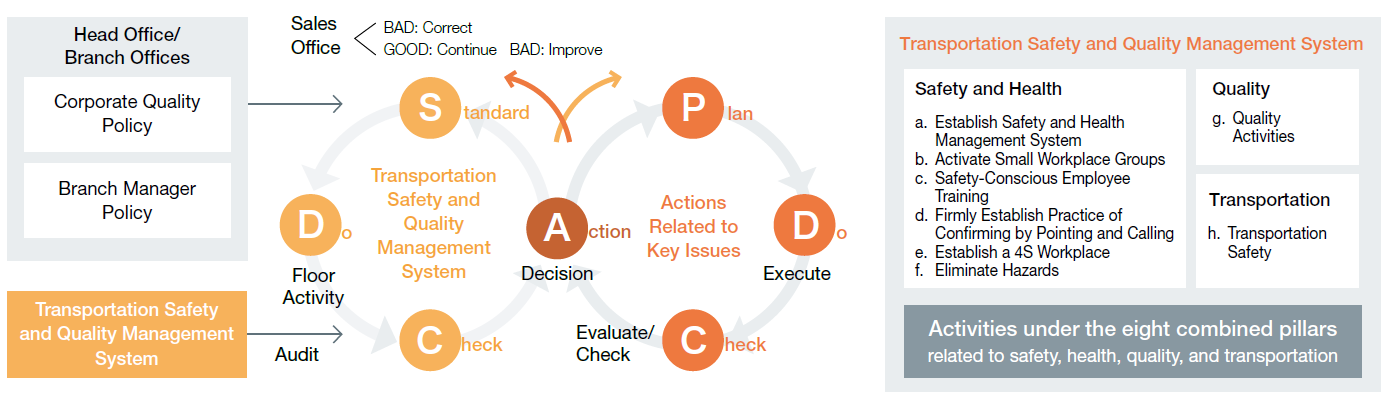
Transportation Safety and Quality Management System
We defined check points for health and safety, quality, and transportation, and confirm the activity status of each sales office based on these check points. This mechanism is our Transportation Safety and Quality Management System. We conduct inspections once a year at the branch office and once every three years at the Head Office. Under the Transportation Safety and Quality Management System, we strive to reduce workplace accidents by checking the status of small-group activities and the practice of confirming by pointing and calling. We also emphasize risk assessments and other front-line activity audits and check for the establishment of a safety management system as required by Japan’s Industrial Safety and Health Act. We divide the standard for certification into three levels to help us visualize the level of safety activities at each office.
1. Basic Policy for Transport Safety
- Our executives understand that transport safety is key to Konoike's operations, and they provide leadership in seeing that it is implemented.
- Our executives constantly stress the paramount importance of transport safety to all employees.
- We are thorough and meticulous in carrying out the plan-do-check-action (PDCA) cycle in all transport safety-related matters, and the entire company functions as one in striving to raise the level of transport safety.
- We inform the public of what we are doing to maintain and improve transport safety.
2. Key Measures
- Foster a strong awareness of the importance of transport safety, and abide by all related laws and company regulations.
- Invest in facilities and equipment that will further transport safety.
- Conduct in-house audits on transport safety and correct any problems discovered during these audits.
- Establish systems for the smooth flow of information related to transport safety, and ensure that all relevant information is shared in-house.
- Carry out education and training on transport safety.
- Implement safety education training for subcontracting companies that have continuous contracts with us.
3. Safety Targets
Through the appropriate operation of the Transportation Safety and Quality Management System, we aim at zero at-fault accidents and zero single-vehicle accidents. The status of automobile accidents is as follows:
Breakdown of Traffic Accidents in FY3/2024 (KONOIKE Group Total)
At-fault accidents: 21 cases
Single-vehicle accidents: 6 cases
Accidents with partial fault: 1 case
(Of which, accidents subject to Article 2 of the Vehicle Accident Reporting Regulations: 0 cases)
- In FY3/2024, there were 0 cases of orders for ensuring transport safety, business improvement orders, business suspension orders, or suspension of the use of vehicles or other transport facilities.
Vehicle Accident Rate for FY3/2024 (Accidents rate per 1,000,000 km of driving)
0.17
- Formula: (number of at-fault accidents + number of single-vehicle accidents + number of not-at-fault accidents with some negligence on our part) / total travel distance × 1,000,000km
Central Health and Safety Committee
The Central Health and Safety Committee meets twice a year, attended by representatives from labor and management. A total of 43 participants attend these meetings, including 27 from the company side such as business division general managers and branch managers, and 16 from the union side, led by the Executive Chairman. In FY3/2024, the first meeting was held in July 2023 and the second meeting was held in December 2023. The first meeting, held in the first half of the fiscal year, focused primarily on the previous fiscal year’s safety performance and accident trends, as well as discussing future issues and initiatives. Members also shared information on amendments to relevant laws, regulations, and the status of labor union activities during the previous fiscal year. At the second meeting during the second half of the fiscal year, participants discussed safety results and accident trends from the first half of the fiscal year, as well as future issues and initiatives. Participants then discussed and decided on the Corporate Quality Policy for the next fiscal year. As in the first meeting, members also shared information on amendments to related laws, regulations, and the status of labor union activities during the first half of the fiscal year.
Safety Experience Education
In FY3/2020, we began providing safety experience education for the purpose of raising individual safety awareness. In this education, people (safely) experience being pinched by real machines, learn to prevent mistakes by using the pointing and calling method, experience tip-over accidents in virtual reality, and experience a simulation of getting hit by a forklift.
The virtual reality training was implemented for the purpose of raising awareness through realistic experiences, especially for inexperienced young employees and elderly employees who tend to experience accidents at higher rates. In addition, we took equipment out into the field to conduct on-site experience-based training for employees too busy with their own work.
Safety Experience Education Course Participants
FY3/2022 | FY3/2023 | FY3/2024 |
---|---|---|
961 | 668 | 1,009 |
Hazard Prediction Using Real Video Footage
Konoike has conducted a number of training programs to date to raise safety awareness. One such training uses virtual reality (VR) to experience falling in the workplace or simulated contact with forklifts. We began conducting hazard prediction training in FY3/2024 to further raise awareness of safety with the awareness of the parties involved. This prediction training analyzes video footage of actual incidents. Training materials includes videos of near-miss incidents experienced by our employees while driving, regardless if they were the cause or the victim. These videos allows each participant to understand the potential dangers in various situations and consider response measures. With drive recorders already installed in all vehicles, we now have access to over 300 videos and endeavor to preventing traffic incidents through this training.
Equipment for Transport Safety
- All vehicles are equipped with daytime auxiliary LED lighting.
- Digital tachographs and driving recorders have been installed in all vehicles. The driving recorders have been upgraded to AI-equipped models by March 2023.
- To detect sleep apnea syndrome (SAS) at an early stage, from fiscal year 2008, we adopted a system under which all drivers undergo diagnosis once every two years continuously.
As an effort for accident prevention measures, we utilize equipment such as Sleep Buster (equipment that prevents one from dozing off), Sleep Scan (ascertains one’s sleep state), and Mobileye (addresses inattentive/drowsy driving) as measures to prevent drowsy driving and accidents from arising due to inattentive driving or health state. - Aptitude Test
In our offices in Chiba, Saitama, Gunma, Ibaraki, Kanagawa, Aichi, Osaka, Wakayama, and Kumamoto, we have installed a total of 16 units of NASVA Net, which was developed by the National Agency for Automotive Safety and Victims’ Aid, and conduct aptitude tests for drivers.
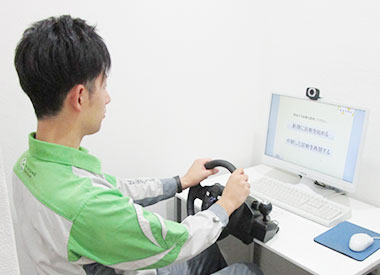
Driver Contest

Initiatives for Employee Health
Stress Checks and Mental Health Care
The KONOIKE Group conducts stress checks in accordance with legal requirements. If a stress check results in a report, we hold an interview with an industrial physician and strive for improvement. To improve mental health, we established a system in which two employees at each sales office, having obtained certifications in a line care course for mental health, act as contact points to facilitate attentive care for employees in need.
Supervision of the Board of Directors for Occupational Health and Safety
Once a quarter, reports are made at the board of directors on matters related to occupational health and safety. The number of workplace accidents is analyzed by sorting them by the number of occurrences, years of work experience of the victims, type of workplace accident, and other factors. This analysis is used to report on workplace accident trends for the quarter in question and initiatives for the next quarter given these trends. Analysis is also conducted for automobile incidents by the number of occurrences, type of injury or damage, type of commercial or business-related vehicle, and type of owned or outsourced vehicle. This analysis is used to report on matters to be addressed in the next quarter based on incident trends for that quarter. Reports are similarly made for quality incidents.
Work-Related Accident Data (KONOIKE Group Totals)
Number of Accidents
- The number of automobile accidents includes cases of damage.
Rate of Incidents/Rate of Lost Worktime Incidents
Quality Initiatives
Initiatives for Customer Satisfaction
Quality is a very important factor in building relationships of trust with customers. Accordingly, we have been pursuing K-QMS (KONOIKE Quality Management System) activities. By listening during customer visits and through customer communications, we identify customer needs, set goals at the beginning of the year, and confirm progress in our Transportation Safety and Quality Management System. After taking corrective measures and measures against recurrence for problems that arise at an operating location, we share information about the incident throughout the Company via corporate intranet to prevent recurrence of similar issues.
Developing Internal Auditors
Under our K-QMS program, sales offices conduct internal audits on each other. The purpose of internal audits is to confirm operating conditions. For example, audits determine whether the established K-QMS conforms to customer requirements, laws, and regulations and whether it is effective. Because it is so important to give internal auditors the knowledge needed to conduct these audits, the Head Office Safety/Quality Department organizes internal auditor development trainings once a year.
Safety and Quality Activity Presentations
A group-wide event is held each April to present reports on safety and quality activities. During the event, there are presentations about particularly excellent activities from the previous fiscal year and chances to share information about initiatives with all employees. The approximately 200 offices and affiliates in Japan engage in preliminary competitions within their respective branches and affiliates, with the selected winning groups from each advancing to a meeting of their respective business divisions. Those winning at their business division meetings advance to the group-wide meeting. Eight groups in total made presentations of their activities in FY3/2024. That included two presentations on safety, one on quality, and five on increasing productivity.
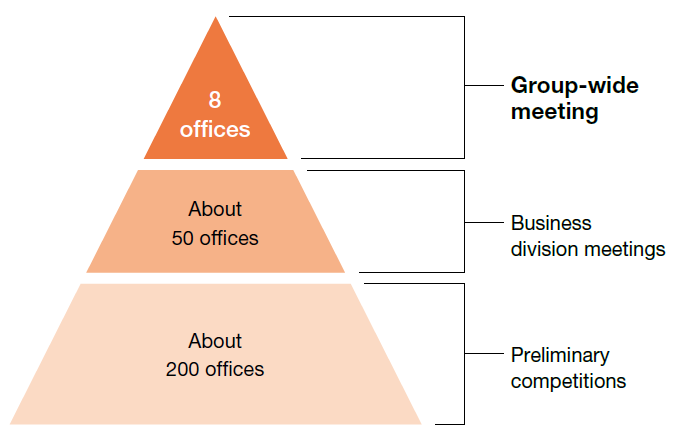
Internal Award System
Each year on the day in May set aside to commemorate KONOIKE’s founding, we present awards to offices and individuals that have made outstanding contributions to transportation safety and quality, as well as offices that have demonstrated excellence in their activities. For FY3/2024, 23 offices and individuals were honored in the safety category, 44 in the transportation category, 36 in the quality category, 19 in the distinguished service category, and 41 in the excellence activities category.
Activities With Our Clients
Building Relationships With Our Clients
It is essential that we collaborate with our partners in carrying out our work. We engage in active communication with our partners to align our approaches regarding safety and quality improvements. Each sales office holds councils with partner companies, conducts safety activities addressing the same topics as their partner companies, and strives in other ways to perform coordinated activities. Each year, sales office representatives also visit partner companies to share information about safety activities, quality activities, and the status of legal compliance. In this way, we ensure that both the KONOIKE Group and our partners continue to improve. During these visits, representatives confirm the management policy, business plan, transport management, driver and vehicle management status, and safety activities for each trucking company based on the Partner Management System Evaluation Table. For partner companies working with us as on-site contractors or dispatchers, we also check their legal documents, insurance coverage, employment contracts, and health and safety activities. Visits were made to 300 partner companies in FY3/2024.
Activities with Our Communities
Watching Over Children on Their Way to and From School
Our sales offices located near elementary schools are engaged in activities to watch over children on their way to and from school. Timed with the beginning and end of classes, employees stand along routes to and from school to assist elementary school students as they cross crosswalks. As a logistics company that uses trucks, we work with local police, municipalities, and elementary schools to ensure the safety of children on a daily basis.
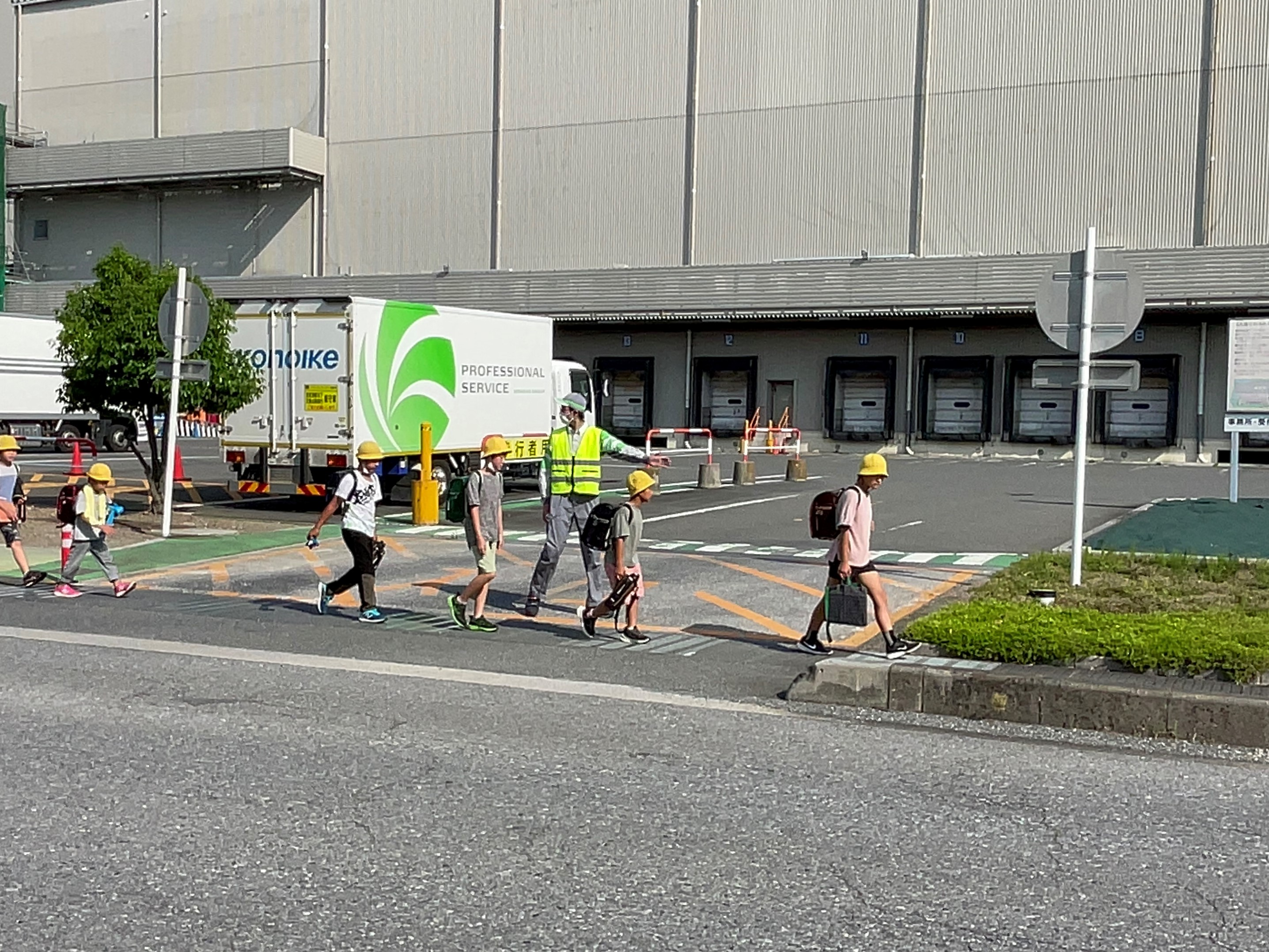
0905.jpg)
Truck Ride Events
Since 2019, we have been holding truck ride events for children in locations across Japan to raise awareness and eradicate traffic accidents. Children sit in the truck driver’s seat to learn about blind spots with their own eyes. We also hold a traffic safety class to explain the difference between the inner wheels of trucks and the relationship between speed and braking distance.
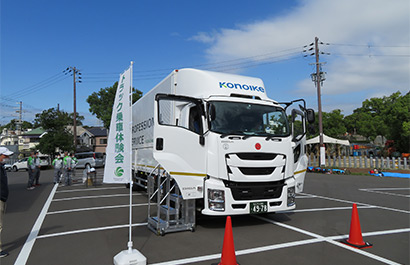
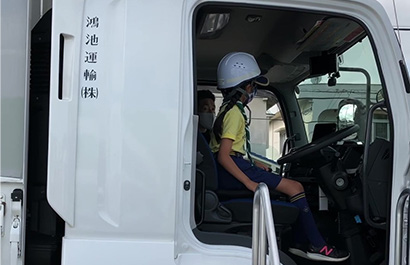